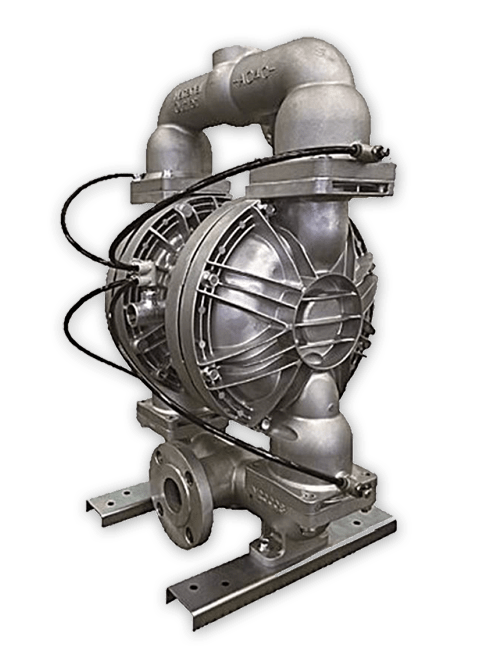
Portable Powder Pumps
Specially designed and engineered AODD Powder Transfer Pumps are used to effectively transfer very fine, dry and low bulk powders safely, cleanly, and economically. Powder pumps create a safe, efficient and dust-free work environment. They can eliminate the need for intensive physical labor & heavy lifting. A cost-effective replacement for all types of powder augers, mechanical conveyors, screw feeders and pneumatic conveying systems.
To operate efficiently, the Powder Material must be completely dry, fine-grained, free-flowing and with low bulk density. The powder is fluidized inside the pump, therefore powder that cannot be fluidized, cannot be transferred. The conveying distance will depend entirely on the type of powder, its weight, size, shape and bulk density. Typically powders such as Pigments, Activated Carbon, Powder Coatings, Carbon Black, Fumed Silica, Talc, Toners & Powdered Plastics can all be transferred successfully. However, a trial should always be carried out to determine the pumps ability to transfer a certain types of powders.
Key Features and Benefits of Powder Diaphragm Pumps
- 100% Pneumatic Operation: These powder diaphragm pumps operate entirely on pneumatic power, eliminating the need for electrical components.
- Portable and Easy to Use: Designed for ease of use, these diaphragm powder pumps are portable and user-friendly.
- Comes Fitted with a Compressed Air Induction System: Each pump comes fitted with a system designed to fluidize (aerate) the powder, making it act like a liquid for easy transfer.
- Compact & Robust Construction: The dry powder pumps are built to be durable and space-efficient.
- Wide and Sturdy Base: Ensures stability during operation.
- Outside Accessible Air Motor: Allows for easy maintenance.
- 100% Non-Lubricated Air Motor: Ensures clean operation without the need for lubrication.
- Designed for High-Performance Operation & Long Life Expectancy: Engineered for high performance and a long life expectancy.
Operational Requirements for Diaphragm Powder Pumps
To ensure the pump operates efficiently it’s important that the powder material is finely ground, able to flow freely and has a low bulk density. The powder moves like a fluid, inside the pump so powders that can’t flow like a fluid cannot be transferred. The distance the powder can be conveyed depends on factors such as the type of powder its weight, size, shape and bulk density. Generally speaking, powders, like pigments, activated carbon, powder coatings, carbon black, fumed silica, talc, toners and powdered plastics can be successfully transferred. However, it’s always advisable to conduct a trial to assess if the pump can effectively transfer types of powders.
About Compressed Air Induction System
All Powder Pumps are fitted with an externally mounted Air Induction System. This system is designed to Fluidize (Aerate) the powder. Once in a Fluidized State, the powder will act like a liquid and can be easily transferred. Air fluidization is controlled by individual Air Valves situated on each of the incoming compressed air lines.
Additional IWAKI AIR Powder Pump Information
- Powder Pumps are available in ¾” 1” 1½” 2” & 3” Aluminium or Stainless Steel
- Shipped with factory fitted Compressed Air Induction System
- The standard model utilizes 4 inlets however custom models are available
- Please consult Iwaki America for more information about pumping powders
Choosing the Right Powder Diaphragm Pump for Your Needs
Selecting the appropriate powder diaphragm pump involves a careful analysis of several factors.
Type of Powder: The nature of the powder being handled is paramount; considerations such as particle size, shape, weight, and bulk density are crucial. For instance, powders with very fine granules and low bulk density are typically more manageable and can be fluidized more efficiently.
Applications: It’s also important to consider the operational environment. For applications in food processing or pharmaceuticals, a stainless steel pump might be necessary to meet hygiene standards. On the other hand, aluminum pumps may suffice for industrial applications where hygiene is less critical, but cost efficiency is a priority.
Requirement: Lastly, the specific requirements of the conveying system must be considered. This includes the distance the powder needs to be transported, the required flow rate, and the compatibility with existing systems. Consulting with experts, such as those at Iwaki America, can provide valuable insights and help in selecting a pump that meets all operational needs while ensuring efficiency and reliability.
Applications of Diaphragm Powder Pumps
Diaphragm powder pumps are widely utilized in a variety of industries.
Pharmaceutical Industry: These pumps play a role in transferring powders used in drug production ensuring accurate and contamination free handling.
Food & Beverage Industry: In the food sector these powder transfer pumps are highly beneficial for transferring ingredients such as spices, flavorings and additives that require hygienic handling.
Cosmetics Industry: In cosmetics manufacturing powders like talc and pigments are efficiently and securely transported to maintain product integrity.
Various types of powders such as activated carbon, fumed silica and powdered plastics are managed by these pumps across industries. The ability of these pumps to ensure a clean and dust free transfer enhances safety and efficiency in all applications.
Moreover, these pumps are adaptable to various specialized applications, including the transfer of sensitive materials in electronics manufacturing, where avoiding contamination is critical. The versatility and reliability of diaphragm powder pumps make them indispensable tools across these diverse fields.
Maintenance and Longevity of Powder Diaphragm Pumps
Maintaining powder diaphragm pumps is essential for ensuring their long-term performance and reliability. Regular maintenance involves inspecting and cleaning the air motor, checking for any wear and tear, and ensuring the compressed air induction system is functioning correctly. The non-lubricated air motor design simplifies maintenance by eliminating the need for lubrication, reducing downtime and operational costs.
To extend the lifespan of the pumps, it is crucial to follow the manufacturer’s guidelines for operation and maintenance. This includes using the pumps within their specified capacity and ensuring the powder being transferred meets the required criteria for fluidization. Regularly checking the air valves and other components for blockages or damage can prevent potential issues and maintain optimal performance.
Implementing a scheduled maintenance routine and training personnel on proper handling and maintenance procedures can significantly enhance the longevity and efficiency of the pumps. By prioritizing maintenance, businesses can ensure continuous, reliable operation, minimizing the risk of costly breakdowns and maximizing the return on investment.
Get Social